製品表面の微細なキズ・汚れを正確に判定
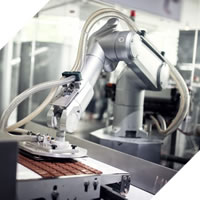
画像処理を活用した製品検査・外観検査装置をご提案しているアイエスシー株式会社がキズ・汚れ検査についてご説明します。キズ・汚れ検査とは、金属や部品樹脂材料の表面に付いたキズや汚れを判定する工程です。 特に部品などは、製造物に組込まれた後、時間が経過した時点で致命的な障害を発生する要因にもなり、安全に対する要求は非常に厳しさを増しています。そのため生産現場のニーズに応え、消費者の元へ安全な製品を届けるために必要な道具としてキズ汚れ検査機があります。こちらでは、当社がご提案しているキズ・汚れ検査の手法や検査可能項目、使用用途、検査の流れについてご紹介します。
検査の手法
キズ・汚れ検査では、主に製品の表面に付いたキズ・汚れを自動で判別します。素材は金属や樹脂、木材など問わず、さまざまな製品に活用できる技術です。また、2次元計測では素材表面のキズ・汚れしか判別できませんが、3次元計測を組み合わせることで高さの変化も検知可能です。これによってクラックや欠け、また穴などの検知も可能です。
2次元計測 |
---|
カメラで撮像した画像を解析し、製品表面に付いたキズ・汚れなどを検知可能です。計測精度は1μmなので、目視で見逃してしまうような微細なキズ・汚れも発見できます。 |
![]() |
3次元計測 |
---|
撮像したデータを解析することで、高さの変化を検知することができます。これによって製品表面のクラックや欠け、穴などを判別可能です。 |
![]() |
検査動画
シャフトキズ検査システム
ガラス表面キズ検査システム
検査可能項目
キズ | 汚れ | 欠け |
穴 | クラック | バリ |
使用用途
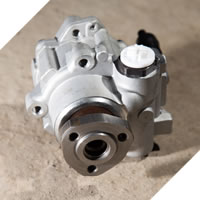
キズ・汚れ検査では、金属や木材、樹脂などさまざまな素材表面に付いたキズ・汚れを検知可能です。こちらでは、代表的な活用例をご紹介します。

- 金属表面に付いたキズ・汚れ・欠け・穴の判別
- 木材のキズ・節目・割れなどを欠点検出検査
- シャフト表面の傷、打痕等の不良の検出・自動判別
- バネ(自動車のサスペンション)のクラック検出・バネの品質向上
検査の流れ

- 01撮像
- センサーで対象物を撮像します。


- 02切り出し処理
- 画像データから検査に必要な部分のみを切り出します。


- 03前処理(ノイズ除去)
- 切り出した画像のノイズを除去し、鮮明な画像に補正します。


- 04形状検査
- キズや汚れ、欠け、穴などを計測します。


- 05判定結果
- 測定基準に適合しているか判定します。
アイエスシーの開発実績
【事例1】バネクラック検査装置
目的 | 車載サスペンション用バネ部品の製造工程において発生するクラックの自動検出を目的とし、バネ製造工程に本装置をインライン化する事により、バネ部品製造の品質向上を行う。 |
---|---|
外観 | 検査環境は対象バネが高温になる為、検査機構は高温対応で、放熱も考慮しています。 |
手順 | ①供給コンベア(搬送網コンベア)から供給位置にセットしロボットハンドで検査ヘッドに移送する。 ②検査ステージはSUS製のローラー2本で構成され、ローラーはモーターによって回転。 ③検査ステージはバネを回転しながら移動中に検査を行い検査後、移動コンベアに載せたまま、判定結果により搬送先を振り分ける。 |
---|
【事例2】レーザー計測による金属部品傷検査
対象 | 金属部品の形状及び表面の打痕傷等を検査 ●検査対象部 1.1 部品外周部のバリ、打痕 1.2 部品表面(表裏)の傷 1.3 部品の3か所の内径部のバリ、打痕 |
---|---|
方法 | 計測方法は、レーザーカメラにより対象部品を光切断法にて計測を行う。 計測した情報は、プロファイルとして保存され、プロファイルの内部情報を分析する事により表面の高さ情報を利用し、高さ情報が急激に変化する部分について、正常品の数値と比較し異常値であった場合は、検査結果としてNGを発生する。 |
検査項目から探す
アイエスシー株式会社では検査項目に合わせて、画像処理システムを利用した製品検査・外観検査装置をご提案可能です。まずはお気軽にご相談ください。