正確な寸法や位置と比較しながら不良品・NG品を判別
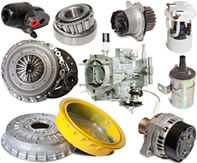
画像処理システムを活用した製品検査・外観検査装置をご提案しているアイエスシー株式会社が形状検査についてご説明します。形状検査とは、製品の変形やマークのズレなどを判別する工程です。こちらでは、当社がご提案している形状検査の手法や検査可能項目、使用用途、実際の事例などをご紹介します。
形状検査の手法
形状検査では、寸法や打刻・マークの位置といった製品自体の形状に関する不良品・NG品の判別を行います。現在、これらの検査は目視や手作業による計測が主流ですが、センサーといった撮影機材の性能向上や普及により、比較的低コストでも導入できるようになっています。
当社では、2次元および3次元計測を使用し、商品や検査項目に合わせた自動検査システムをご提案しています。あらかじめ基準となる寸法や位置などを指定することで、形状の異なる不良品・NG品を高精度で判別可能です。
2次元計測 | 3次元計測 |
---|---|
カメラで撮影した画像を解析することで、基準品とのズレや異物などを検出するシステムです。1μm精度で製品表面の形状変化を検知可能です。 | 2台のセンサーで撮像することで高さなどの変化を検知。製品の形状認識やクラックなどの確認を行います。 |
検査可能項目
バリ | 打痕 | クラック |
欠け |
使用用途
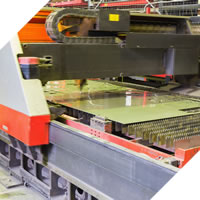
形状検査は、金属製品の寸法や溶接部の不良、樹脂製品の変形、食品パッケージのマークの位置、容器の容積など、さまざまな用途で活用されています。

- 鋼材・金属部品などの寸法および形状計測
- 部品のクラックや溶接部の接合状態検査
- 容器内の容積変化の計測
検査の流れ

- 01撮像
- センサーカメラ・レーザーで対象物を撮影します。


- 02切り出し処理
- 撮影した画像データから検査に必要な部分のみを切り出します。


- 03前処理(ノイズ除去)
- 切り出した画像のノイズを除去し、鮮明な画像に補正します。


- 04形状検査
- 商品の変形やズレなどを計測します。


- 05断面検査
- レーザーによって商品の断面などを検査します。


- 06判定結果
- 測定基準に適合しているか判定します。
アイエスシーの開発実績
【事例1】鋼材寸法計測評価システム
検査装置の目的
鋼材の寸法測定・判定を自動で行う形状検査システムです。ラインセンサーの検査幅は57mmの範囲で、鋼材サンプルが57mm幅を超える場合は2回計測を行います。最終構成では、鋼材の最大幅を測定範囲として、カメラを自動移動させるか、複数のカメラをセットするシステム構成になります。なお、カメラ・ラインセンサーを支えている「やぐら」は、計測物の構成変更に対応できるように移動レール上に設置。移動レールと検査台の長さを変更することで、さまざまな長さの鋼材を計測することが可能です。
![]() |
突起物の場所に関係なく、位置を計測できるように鋼材の上左右の3方向から撮像できるようにカメラを設置します。 |
【事例2】建機ホイール種別判別システム
検査装置の目的
建機ホイールの種別を判定するため、高さや内径などの各部位のサイズを計測。その情報をもとに種別の判断を行います。
![]() |
2台のレーザー装置を図のように配置します。レーザー測定器1はホイールの内側(リム高・ディスク位置・リム内径)を計測。レーザー測定器2はホイールリムの厚みを計測します。 |
![]() |
レーザー計測器から得られた情報をもとに、各種ホイールの中から情報をすべて一致するホイールを判別します。 |
【事例3】鋼板溶接部検査システム
検査装置の目的
溶接部にレーザー光を照射し、接合状態を確認します。レーザーを利用することで目視ではわからない内部状態まで確認でき、一定以上の品質維持が行えます。
![]() |
グラフは画面上の白い線(レーザースキャン部)は変化量を示し、変化量の大きさは溶接部の深さを表しています。実際の画像処理では、カメラから数値情報を受け取り、測定形状の変化を判断して溶接部の状態を判別します。 |
検査項目から探す
アイエスシー株式会社では検査項目に合わせて、画像処理システムを利用した製品検査・外観検査装置をご提案可能です。まずはお気軽にご相談ください。